2005 Iberica JRK-105 Automatic Die Cutter w/ Blanking
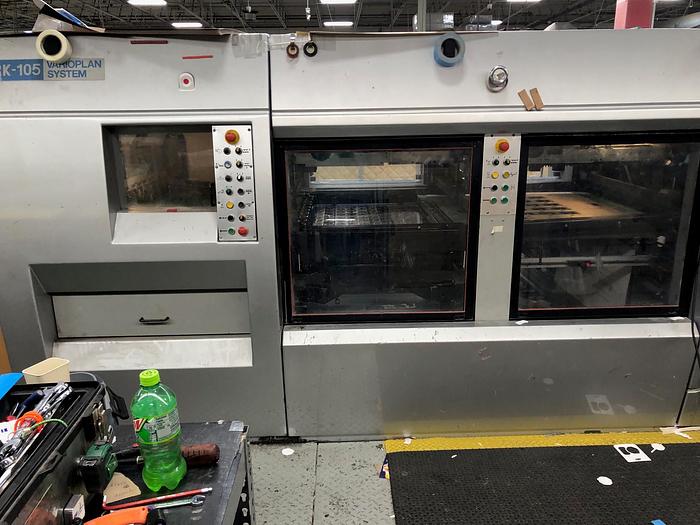
2005 Iberica JRK-105 Automatic Die Cutter w/ Blanking
Contact us for price
Description
Automatic Non-Stop Feeder
Feeding Table
Midline Center System
Stripping Unit
Blanking Unit w/ Automatic Non-Stop Reception
Automatic Non-Stop Delivery
Technical Specifications
Maximum Sheet Size: (750 x 1,050mm)
Minimum Sheet Size: (350 x 400mm)
Maximum Cardboard Thickness: 1.5mm
Maximum Corrugated Board Thickness: 3mm
Maximum Cutting Pressure: 300 tons
Maximum Speed: 8,500 sheets per hour
Conveyance System
The feeder automatically separates the sheets and feeds them down the feed table in a smooth continuous stream. Individual sheets are registered into the grippers which are
manufactured in strengthened materials and aerodynamically designed to avoid excessive air turbulence. There are nine gripper bars which transport the sheets accurately into the
press for cutting and creasing. The cut and creased sheets are delivered into the stripping and blanking units. A system of photocells and electronic devices throughout the machine
control the sheets, detect any faults, and ensure trouble free running.
Automatic Non-Stop Feeder
Designed to handle a range of materials from paper to corrugated board up to 3 mm Thickness. Changeover for different sheet sizes and papers weights is quick and simple. It is equipped with a Non-Stop device allowing each stack of work to be inserted without stopping the machine. The unit is also equipped with floating platform system and colored guide lines which enables palletized stacks to be used and facilitates easy alignment. A two sheet detector device ensure that sheets are delivered correctly to the feed table.
Feeding Table
The feeding table conveys the sheets from the feeder to the press infeed in a flat and shingled manner. There is a hinged frame mounted on top of the feed table, complete with a
series of transport wheels and brushes, this can be lifted and locked clear of the table for easy access. The feed table is made of Anti-Static stainless steel and is fitted with four Anti-Static conveyor belts, with variable speed which run over the surface, ensuring perfect control of the sheets to the front lays. The front lays are individually adjustable. The side lays
are adjustable for all sizes and move on a calibrated scale guide to facilitate the change over from one job to the next. The side lays are able to operate in either a pushing or pulling
action, according to the caliper of the board. There is an electronic sidelay register control device.
Main Control Panel
The main control panel is situated adjacent to the feed table and incorporates a schematic of the machine with lights indicating the position of any malfunction within the machine, other auxiliary controls are located in the feeder, stripping and blanking unit, to allow the operator to perform each task.
Press
Special heavy duty casting and high quality materials are used in the manufacture of this section to ensure long life and vibration free impression. It develops a maximum pressure of 300 Tm accurate pressure setting to 1/100 Mm (.0004') is adjusted by means of a handwheel. The moving lower platen is driven vertically on four elbow levers by the VARIOPLAN SYSTEM, producing a long and even pressure. Automatic lubrication ensures smooth operation and minimum wear. Rotating arms enable the formed to be swiveled thus providing easy access for any corrective work to be carried out. An automatic stop device allows the machine to be stopped in the exact position to remove chases and cutting plate. A midline center system allows the quick Set-Up of the form in the chase.
Stripping Unit
Automatic stripping of the waste is effected in this unit, which incorporates three removable chases equipped with cross-bars and pins. The upper chase is motorized and can be raised vertically whilst the machine is stationary. The upper chase and female chase incorporate the midline center system for quick Set-Up. In order to take out the stripping chases, you depress a button to stop the machine automatically in the correct position. The stripping unit can be prepared off the machine with the pre-make ready stripping table as an option.
Blanking Unit
This unit separates the blanks from the waste. The blanks are pushed down into the lower blank separating tool, leaving the remaining waste to continue onto the waste conveyor
delivery belt. The unit is equipped with two chases, an upper and lower chase, which enables the separating tools to be set quickly. Both chases can be removed from the machine. Universal tools or specific tools can be completely Set-Up off the machine in the pre-make ready blanking table. The cut blanks are stacked in this unit using a programmable counter to pre-determine the amounts required between interleaving.
Pre-Make Ready Stripping & Blanking Tables
Appropriate for avoiding down-time in preparing the machine with a consequent increase in productivity. The stripping pre-make ready table is equipped with a complete set of chases (upper, female and lower chase) and one complete set of cross bars and pins. Upper and lower stripping chases can be operated in the table in order to check correct setting. The table can be rotated for easy access to both lower and upper chases for settings each job. The pre-make ready blanking table is equipped with the upper and lower universal chases with a complete set of bars.
Interleaving Sheet Magazine
The automatic and programmable insertion of an interleaving sheet ensures an accurate count, and the stability of the pile, and is operated without interrupting production by means of
an automatic Non-Stop rack.
Front Edge & Waste Transport, Quality Control Audit
By means of an adjustable variable speed waste delivery conveyor belt. all remaining waste is deposited onto this belt for final waste disposal. The machine is equipped with the facility to pass one cut and creased non stripped sheet through the machine automatically. and with minimum interference to production. This is achieved by pressing a single button on the control panel. This automatically stops the feeder lifts both stripping and blanking upper chases and passes one cut and creased non stripped sheet through the machine onto the variable speed delivery belt for the operator to remove for checking quality. The machine automatically resets to the full stripping and blanking mode and continuous production.
Pallet Extraction
Once the stack has reached its maximum height or the preprogrammed number of sheets an automatic system removes the full pallet sideways from the machine and places another empty pallet in position. This operation is carried out without stopping production by means of an automatic Non-Stop rack which stores the removed blanks or sheets during this process.
At Capital Equipment Solutions, we pride ourselves on being your go-to partner for new and pre-owned printing and packaging equipment, as well as turnkey solutions, including delivery and installation. Our extensive inventory features high-quality, late-model equipment from industry-leading manufacturers such as Muller Martini, Bobst, Brausse, Heidelberg, Komori, KBA, MANRoland Goss, and more. In addition to our turnkey services, our expert operations team can assist with insurance restoration, removals, relocation, and plant liquidation. We’re dedicated to providing you with personalized guidance and comprehensive solutions that cater to your unique production requirements. Don’t forget to explore our full range of offerings on our website, and feel free to reach out to our expert team for any questions or assistance.
Specifications
Manufacturer | Iberica |
Model | JRK-105 Automatic Die Cutter w/ Blanking |
Year | 2005 |
Condition | Used |
Stock Number | 22435430 |